Introduction
In various industries such as aerospace, defense, automotive, and electronics, shock testing is a crucial process to ensure the durability and reliability of equipment and components. Shock testing involves subjecting a product to sudden acceleration or deceleration forces to simulate real-world conditions and assess its ability to withstand mechanical stress. To conduct effective shock testing, a reliable power source is essential to provide the necessary energy for generating shocks. Diesel generators have emerged as a popular choice for powering shock testing equipment due to their robustness, reliability, and ability to deliver consistent power output. This article explores the role of diesel generators in shock testing applications, their key features, benefits, and considerations for selecting the right generator for shock testing operations.
Understanding Shock Testing
Shock testing is a method used to evaluate the performance and durability of products when exposed to sudden and extreme mechanical forces. These forces can be in the form of impacts, bumps, drops, or vibrations, and are typically applied through specialized equipment such as shock testers or shakers. The goal of shock testing is to assess the structural integrity and functional capabilities of a product under conditions that mimic those encountered during transportation, handling, or operational use.
In industries where safety, reliability, and performance are paramount, such as aerospace and defense, shock testing plays a critical role in ensuring that equipment can withstand the rigors of real-world environments. Components such as avionics systems, electronic devices, automotive parts, and military hardware undergo extensive shock testing to verify their ability to operate without failure or degradation under harsh conditions.
Role of Diesel Generators in Shock Testing
Diesel generators are widely used to power shock testing equipment due to their unique characteristics that make them well-suited for this application. The primary function of a diesel generator is to convert chemical energy stored in diesel fuel into electrical energy through an internal combustion engine. This electrical energy is then used to power various devices and equipment, including shock testers, shakers, data acquisition systems, and monitoring instruments.
Key Features of Diesel Generators for Shock Testing
1. Robust and Reliable Operation: Diesel generators are known for their robust construction and reliable performance, making them ideal for powering critical applications such as shock testing. The internal combustion engine of a diesel generator is designed to withstand high temperatures, heavy loads, and continuous operation, ensuring uninterrupted power supply during shock testing procedures.
2. High Power Output: Diesel generators are capable of delivering high power output, making them suitable for driving heavy-duty shock testers and shakers that require substantial energy to generate controlled shocks. The ability of diesel generators to provide consistent power output enables precise and repeatable testing conditions, essential for accurate evaluation of product performance.
3. Fuel Efficiency: Diesel generators are more fuel-efficient compared to gasoline generators, offering cost savings and longer operating durations between refueling cycles. This fuel efficiency is particularly advantageous in shock testing applications where continuous power supply is essential, and extended testing durations are common.
4. Durability and Longevity: Diesel generators are built to withstand rugged environments, extreme weather conditions, and heavy usage, ensuring long-term durability and reliability. The robust components and solid construction of diesel generators contribute to their longevity and minimal maintenance requirements, making them a dependable power source for shock testing operations.
Benefits of Using Diesel Generators for Shock Testing
1. Enhanced Performance and Accuracy: Diesel generators provide consistent and stable power output, enabling shock testing equipment to operate at optimal levels and deliver accurate results. The reliability of diesel generators ensures that testing procedures are conducted smoothly without interruptions or fluctuations in power supply, leading to precise and reliable test outcomes.
2. Versatility and Flexibility: Diesel generators offer versatility in terms of power output capacity, allowing them to accommodate a wide range of shock testing equipment with varying energy requirements. Whether conducting small-scale component testing or large-scale system verification, diesel generators can be sized and configured to meet specific testing needs, providing flexibility in test setup and scalability.
3. Remote Operation Capabilities: Diesel generators can be equipped with remote monitoring and control systems, enabling operators to monitor power output, fuel levels, and system status from a distance. This remote operation capability is especially beneficial in shock testing applications where test environments may be hazardous or inaccessible, allowing operators to manage generator functions safely and efficiently.
4. Emergency Power Backup: In the event of a power outage or grid failure, diesel generators can serve as reliable backup power sources for critical shock testing operations. The autonomous operation of diesel generators ensures continuous power supply to essential equipment, preventing data loss, test interruptions, and potential damage to test specimens during unexpected power disruptions.
Considerations for Selecting a Diesel Generator for Shock Testing
When choosing a diesel generator for shock testing applications, several factors should be considered to ensure optimal performance, reliability, and efficiency:
1. Power Output Capacity: Determine the power requirements of the shock testing equipment, including peak power demands, continuous power ratings, and any additional power needs for auxiliary devices. Select a diesel generator with sufficient power output capacity to meet the energy demands of the entire testing setup, ensuring adequate power supply for consistent and reliable operation.
2. Fuel Efficiency and Consumption: Evaluate the fuel efficiency of the diesel generator in terms of fuel consumption rates, operating costs, and runtime per refueling cycle. Choose a generator with optimal fuel efficiency to minimize operating expenses and maximize testing durations between refills, especially for extended shock testing procedures that require continuous power supply.
3. Size and Portability: Consider the physical dimensions, weight, and portability of the diesel generator to ensure compatibility with the available space in the testing facility and ease of transport. Select a generator that can be easily maneuvered and positioned within the testing area, allowing for convenient setup, reconfiguration, and relocation as needed.
4. 200kw diesel generator for small manufacturing and Emissions: Assess the noise levels and emissions produced by the diesel generator during operation to comply with environmental regulations, safety standards, and workplace noise limits. Choose a generator with sound-attenuated enclosures, exhaust mufflers, and emission control systems to minimize noise pollution, exhaust fumes, and environmental impact in the testing environment.
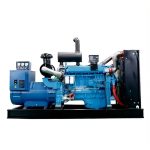
5. Maintenance Requirements: Consider the maintenance schedule, service intervals, and spare parts availability for the diesel generator to ensure ongoing reliability and performance. Select a generator with straightforward maintenance procedures, accessible service points, and reliable technical support to facilitate routine upkeep, troubleshoot issues promptly, and prolong the lifespan of the equipment.
Conclusion
Diesel generators play a vital role in powering shock testing equipment, enabling industries to assess the durability, reliability, and performance of products under extreme mechanical forces. The robustness, reliability, and high power output of diesel generators make them well-suited for shock testing applications where consistent energy supply is essential for conducting precise and repeatable tests. By selecting the right diesel generator based on power output capacity, fuel efficiency, portability, emissions control, and maintenance requirements, organizations can ensure successful shock testing operations, validate product integrity, and maintain quality standards in various industries. Diesel generators continue to be a trusted power source for shock testing, providing the energy needed to push the boundaries of product design, innovation, and safety in today's demanding environments.